1909 - 1967
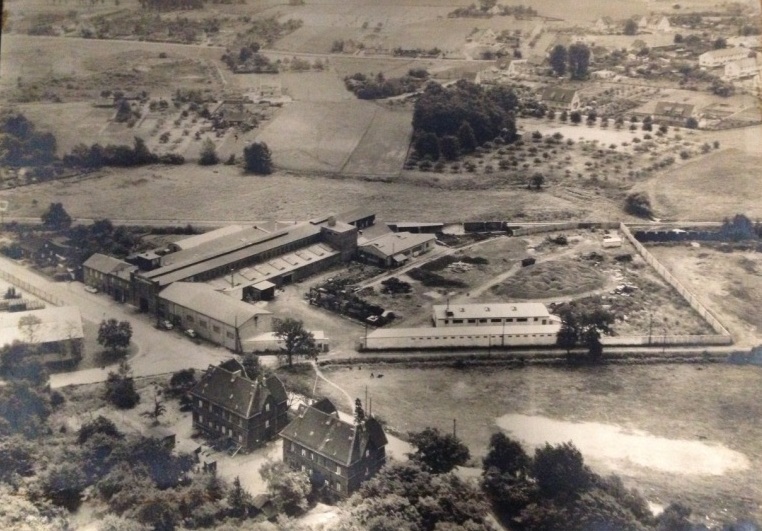
1909
- foundation of the iron foundry Karl Knapp
- 17 employees
- production of castings for mechanical engineering
1919
- leasing of the foundry to Maschinen- und Kranbau AG, Düsseldorf
1933
- closing-up of the foundry due to the economic crisis
1937
- takeover of the company by Emil Sistig OHG
1939
- restart of the foundry with the production of hand-moulded castings and of machine-moulded series parts
1956
- renaming of the company in Lintorfer Eisengießerei GmbH
1962
- start of production of ingot moulds
1963
- installation of a sand preparation plant
1966
- concentration on the production of ingot moulds and accessories
1967
- starting of a 30 t-line frequency furnace and closure of the cupola furnace
1968 - 1996
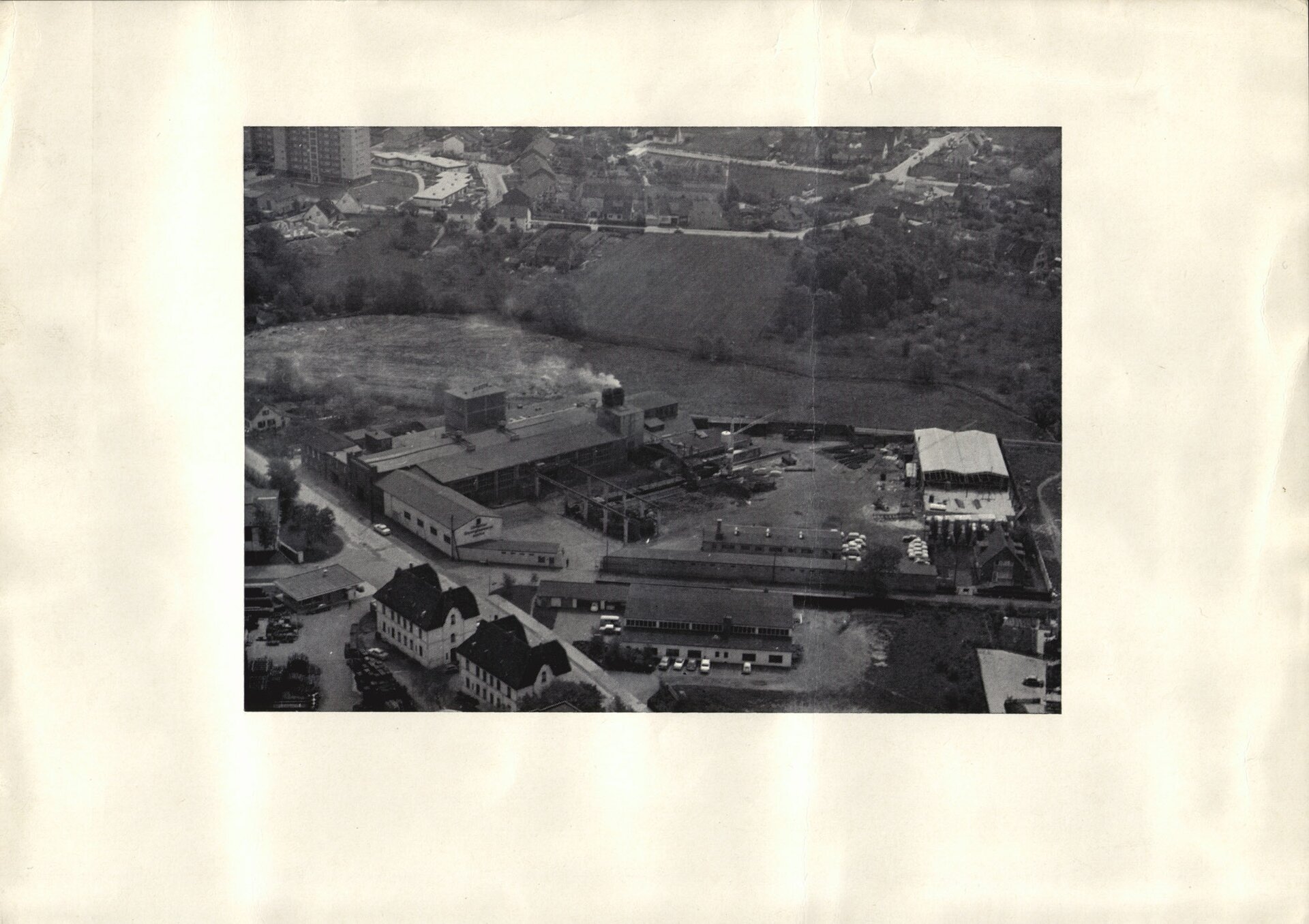
1969
- acquisition of Lintorfer Eisengießerei GmbH by Rheinstahl Hüttenwerke AG
from 1970
- intensified development of ingot moulds of nodular cast iron with increasing share in production
1973
- takeover of the Rheinstahl group by August Thyssen-Hütte AG
1979
- installation of a GF-converter for magnesium treatment
from 1980
- well-directed extension of circle of customers, especially within the West European countries
1991
- starting of an additional line frequency furnace of 12 t
up to 1994
- extension of the capacity to 20.000 t per year
1995
- installation of a new 20 t crane within the moulding shop and casting area
- starting of a new moulding mixer in the mould shop with a capacity of 40 t per hour
1996
- exchange of a milling machine
- starting of a new moulding material mixer in the core shop with a capacity of 20 t per hour
1997 - 2002
1997
- certification according to DIN EN ISO 9002 by TÜV Rheinland
1999
- certification according to DIN EN ISO 9001:1994 by TÜV Rheinland
- renovation of sand preparation plant
2000
- for expansion of machining capacity installation of a further machine centre with installation of a boring and milling machine
- erection of a further warehouse for extremely long pattern equipment
- renovation of compressed-air plant
- starting of production of ingot moulds and accessories of special cast iron with a higher carbon content
2001
- exchange of a milling machine
- installation of a new laboratory
- acquisition of Lintorfer Eisengießerei GmbH by DIHAG Deutsche Giesserei- und Industrie-Holding AG
2002
- renovation of the filtering plant at melting shop/sand preparation plant
2003 - 2017
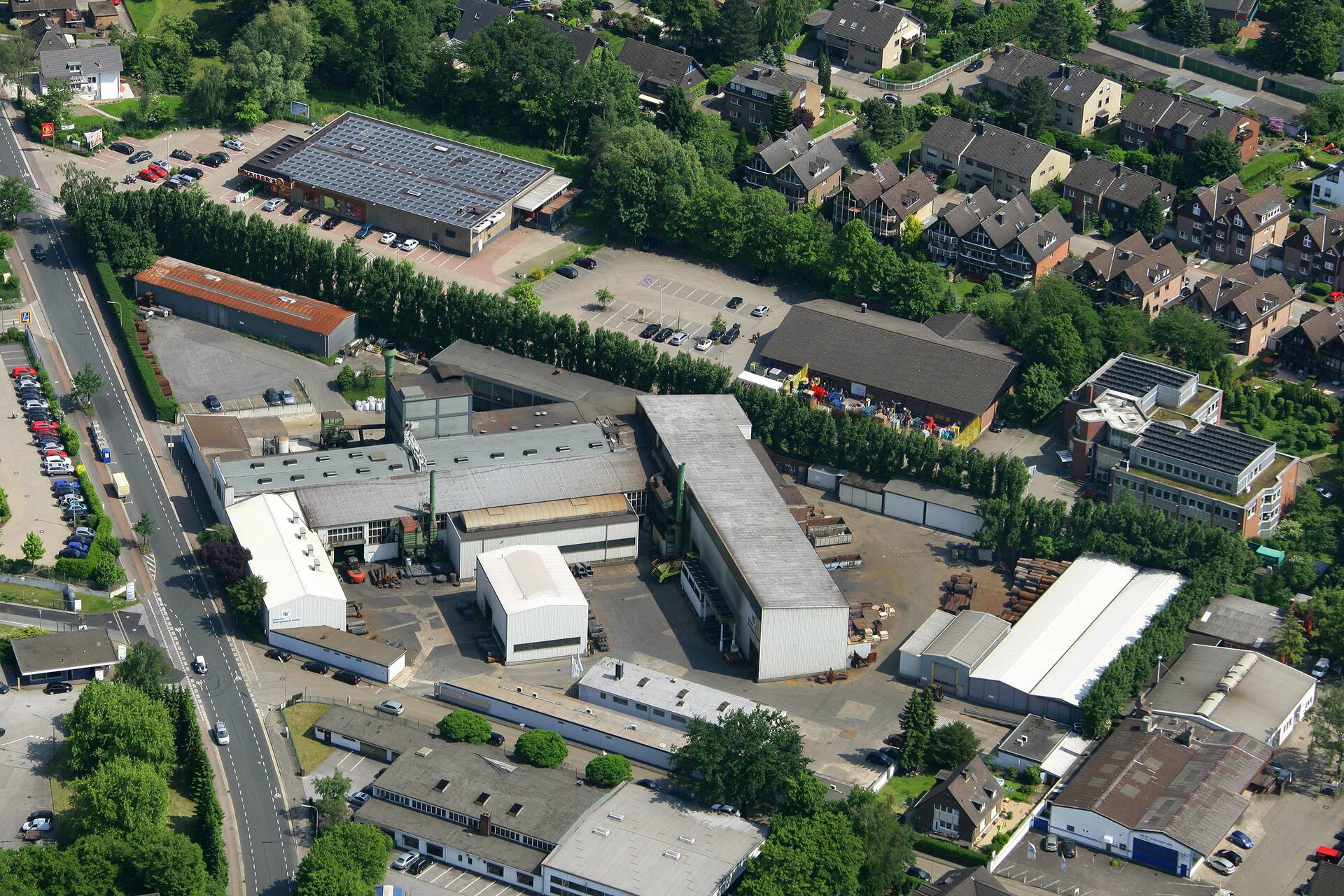
2003
- installation of a warehouse for patterns and accessories
- certification according to DIN EN ISO 9001:2000 by TÜV Rheinland
- installation of a new water cooling
2005
- installation of a new converter
2007
- modernization and modification of the frequency furnace to 32 t for the capacity increase
- construction of a production hall for the extension of the moulding facility for manufacture of accessories
- installation of a new 32 t crane in the moulding area
- increase of capacity to 24.000 t
2008
- certification of the environmental management system DIN EN ISO 14001:2004 byTÜV Rheinland
2009
- installation of a hall for machining and acquisition of a CNC controlled drilling and milling machine
- re-certification according to DIN EN ISO 9001:2008
2010
- start of operation of a second CNC controlled drilling and milling machine
2011
- installation of a new laboratory including a new spectrometer
2012
- acquisition of the DIHAG group by a Swiss investment group
- re-certification according to DIN EN ISO 9001:2008
- supervision audit according to DIN EN ISO 14001:2004
- upgrade audit in the context of the supervision audit according to DIN EN ISO 50001:2011
2013
- expansion and modernization of the fettling shop
- replacement of two pouring cranes 25 t and 30 t
- charging of four further cranes
- supervision audit according to DIN EN ISO 9001:2008
- re-certification according to DIN EN ISO 14001:2004
- supervision audit according to DIN EN ISO 50001:2011
2014
- replacement of a crane
- supervision audit according to DIN EN ISO 9001:2008
- supervision audit according to DIN EN ISO 14001:2004
- re-certification according to DIN EN ISO 50001:2011
2015
- replacement of water and sewage system
- re-certification according to DIN EN ISO 9001:2008
- supervision audit according to DIN EN ISO 14001:2004
- supervision audit according to DIN EN ISO 50001:2011
2016
- supervision audit according to DIN EN ISO 9001:2008
- re-certification according to DIN EN ISO 14001:2004
- supervision audit according to DIN EN ISO 50001:2011
2017
- roof replacement of the main nave of the foundry
- supervision audit according to DIN EN ISO 9001:2008
- supervision audit according to DIN EN ISO 14001:2004
- re-certification according to DIN EN ISO 50001:2011